
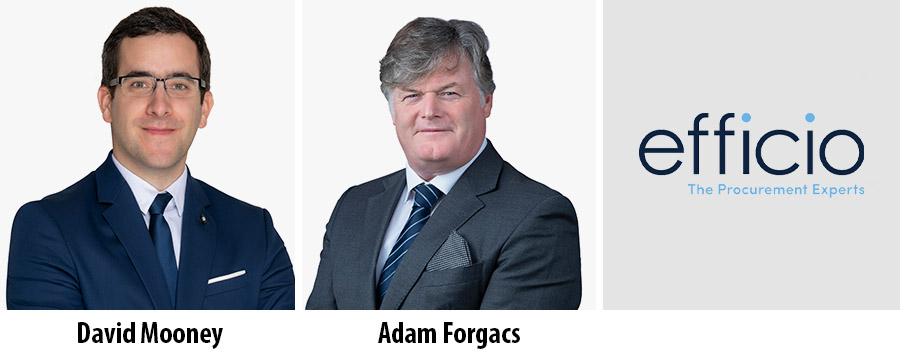
There is a little built in container to catch punching "biscuits" that can be filled with water to cool them as they drop out. This lets you use the space in between to brace a piece being upset using a swage block or floor anvil. The base is cut to fit around the anvil feet. This stand has some handy and unique features. Although the legs have no diagonal bracing it is made of very heavy angle iron that is very stiff (3/8" x 4 x 4) and a piece of 1/2" steel plate. It will end up embedded in either surface and leaning precariously. But you don't want to use this on soft ground or asphalt due to the lack of feet. It may be a light duty stand for close detail work.

It appears (see addendum) to be too tall for general work so On stands of this sort that I have used the anvil bounced around and made clanking sounds. The legs are spindly, and there are no diagonals or feet. I use sheet rock nails on the plywood because they have large heads and anti-pullout ridges. The plywood is also nailed to the 2x4's from the inside. I glue and nail all the joints including the plywood.

Other stands I built the same day were 18" for smaller anvils. This stand is approximately 17" tall to fit me and the large anvil. I usually measure this as 1.5:18 or 2:18 in inches as I layout the lumber. The angled side is 4 to 6 degrees from square. A 2x4 reinforces and stiffens the bottom edge of the plywood. Two sides are 2x12 and the other two are covered with 1/2" plywood. A 200 pound anvil leaves a little space around the edges. But 2 x 12 seems to work best for most anvils. This stand is built from 2x10 or 2x12 (nominal construction size) lumber depending on the size anvil you have. I have used these stands on all sorts of surfaces ranging from concrete to soft wet ground. The hollow center also helps it sit flat on uneven surfaces. I can not tell it from a solid section of log in use. This is a hollow light weight stand that is VERY solid. When this photo was taken for a magazine I had not put the blocks on that keep the anvil in place. This is the style of stand I have been using for 28 years. There are a lot of ways to adapt this design to suit yourself. The tool holding strap could also be a strip of hardwood. To create the right fit you may need an extra "shim" made of plywood so the stack of lumber comes out the proper dimension to fit your anvil.
#Anvil stand with vise how to
In my drawing I show how to do it if you have an even number of boards and the ends do not come out the same. Steve attached a metal strap to make "pockets" to hold tools. The threaded rod actually clamps the anvil in place. There are no nails or shims and the anvil sits on a bed of silicone caulking (really If you look at the ends of the anvil stand you will notice the 1/2" threaded rods that hold the thing together. I suggest using yellow carpenter's glue and glue coated nails. I'd forgotten that Steve's end boards were 1-1/2" taller than the others to retain the anvil.Įach board is offset about 1-1/2 to 2" as they are stacked up. NOTE: When I was making my drawing below I had not looked at this photo for a year. The unique and HANDY thing about this design is the offset Steve put in the pieces as he stacked them up. It is a solid section built up by laminating pieces of 2x12 framing lumber. This anvil stand was built by Steve Barringer of B2 Design in Mooresville, NC. There are numerous ways to build an anvil stand. OR have them available when we NEED a stand. Often after wind or ice storms you can have your choice of log sections if you ask and have a way to haul them home.ĭon't forget that a taller section of log is a handy stand for a swage block OR to carve depressions in the end for forming sheet metal.īut, we are not always so lucky to have windfalls of large logs available OR the chain saw to cut to size. The piece of oak was collected after an ice storm. This old German anvil is setting on an oak stump that was trimmed to fit. Most modern smiths prefer some degree of portability. When you do this you want to be VERY sure that you will not want to change your anvil location. In old shops with permanent forge and anvil locations longer sections of logs like this were often set deep in the ground. I prefer to be able to lift mine off the stand if needed. Some smiths strap their anvils down to reduce the ring. Usually there are some spikes driven in the stump to keep the anvil from walking off from vibration. This is a short section of log that sets on the ground and the anvil sets on top. The Peter Wright anvil on a red oak stand at top is a classic.
